Comprehending What is Porosity in Welding: Causes and Solutions
Comprehending What is Porosity in Welding: Causes and Solutions
Blog Article
The Science Behind Porosity: A Comprehensive Overview for Welders and Fabricators
Comprehending the complex devices behind porosity in welding is crucial for welders and producers pursuing impeccable workmanship. As metalworkers delve into the depths of this sensation, they reveal a world controlled by numerous variables that affect the development of these tiny voids within welds. From the make-up of the base products to the details of the welding procedure itself, a multitude of variables conspire to either aggravate or ease the visibility of porosity. In this detailed overview, we will certainly decipher the scientific research behind porosity, discovering its results on weld high quality and unveiling advanced strategies for its control. Join us on this trip with the microcosm of welding flaws, where precision meets understanding in the pursuit of perfect welds.
Recognizing Porosity in Welding
FIRST SENTENCE:
Assessment of porosity in welding discloses essential understandings into the honesty and quality of the weld joint. Porosity, defined by the presence of tooth cavities or gaps within the weld metal, is a common concern in welding procedures. These gaps, if not appropriately resolved, can endanger the architectural honesty and mechanical properties of the weld, resulting in prospective failings in the finished item.
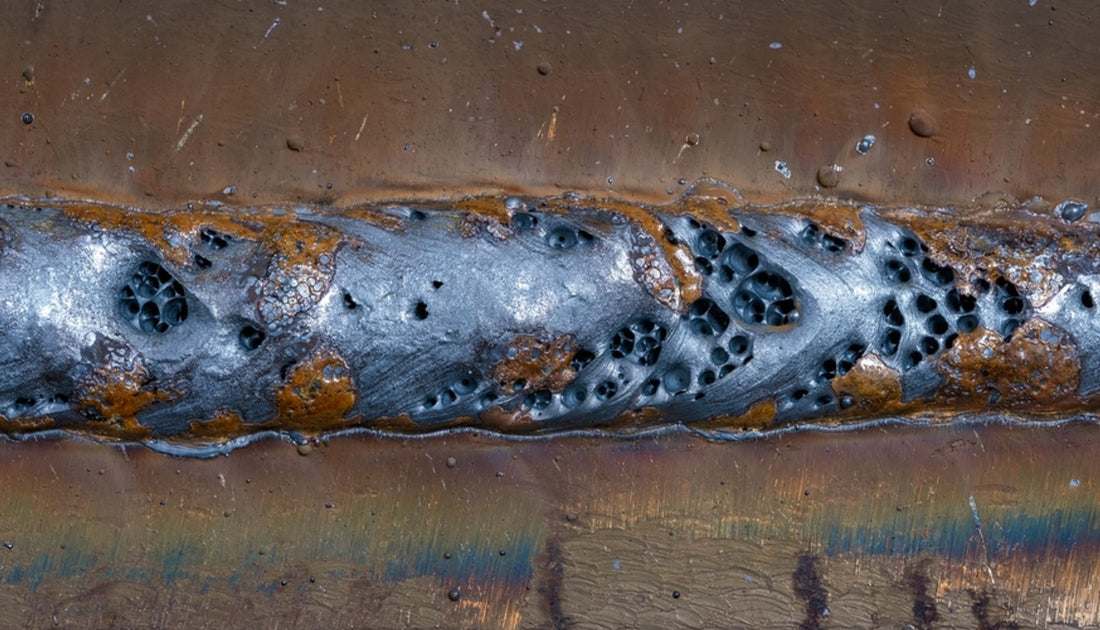
To spot and quantify porosity, non-destructive testing approaches such as ultrasonic screening or X-ray examination are usually used. These methods enable for the identification of internal issues without endangering the stability of the weld. By analyzing the size, shape, and circulation of porosity within a weld, welders can make enlightened decisions to improve their welding procedures and attain sounder weld joints.
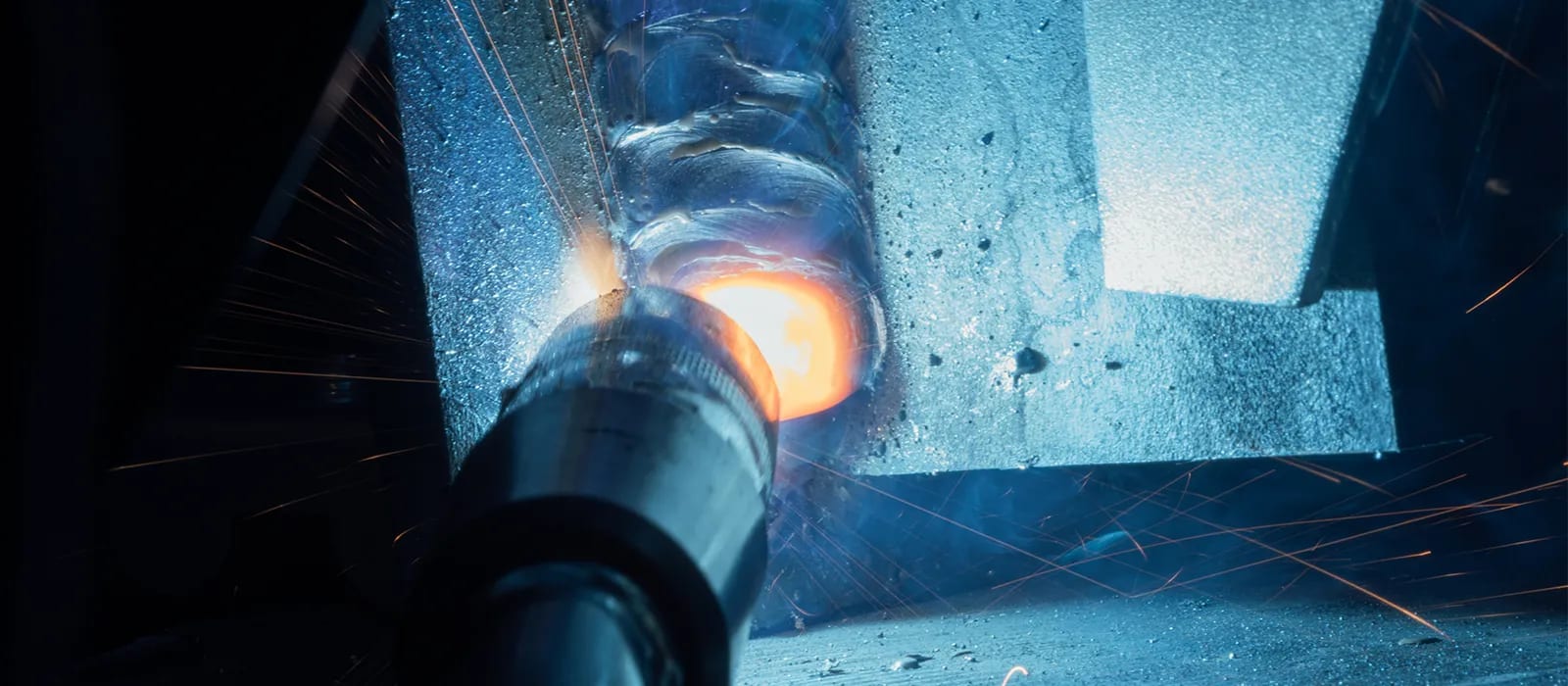
Variables Influencing Porosity Formation
The occurrence of porosity in welding is affected by a myriad of factors, ranging from gas shielding effectiveness to the intricacies of welding parameter settings. Welding parameters, including voltage, current, travel rate, and electrode kind, additionally effect porosity formation. The welding method utilized, such as gas metal arc welding (GMAW) or shielded metal arc welding (SMAW), can affect porosity formation due to variants in warm distribution and gas protection - What is Porosity.
Effects of Porosity on Weld Quality
The presence of porosity likewise deteriorates the weld's resistance to deterioration, as the trapped air or gases within the spaces can respond with the surrounding setting, leading to destruction over time. Additionally, porosity can impede the weld's capability to hold up against pressure or impact, additional endangering the total top quality and reliability of the welded structure. In crucial applications such as aerospace, vehicle, or architectural constructions, where safety and resilience are vital, the damaging results of porosity on weld top quality can have severe repercussions, highlighting the significance of lessening porosity with appropriate welding methods and procedures.
Methods to Reduce Porosity
In addition, using the ideal welding specifications, such as the correct voltage, present, and travel speed, is crucial in stopping porosity. Maintaining a constant arc length and angle during welding additionally helps minimize the likelihood of porosity.

Making use of Get More Information the suitable welding method, such as back-stepping or employing a weaving movement, can also help distribute heat evenly and reduce the chances of porosity development. By implementing these strategies, welders can successfully lessen porosity and generate premium bonded joints.

Advanced Solutions for Porosity Control
Applying sophisticated innovations and innovative methods plays a crucial function in achieving premium control over porosity in welding procedures. One advanced remedy is making use of advanced gas mixtures. Protecting gases like helium or a mix of argon and hydrogen can help minimize porosity by offering far better arc stability and boosted gas protection. In addition, utilizing innovative welding methods such as pulsed MIG welding or changed environment welding can additionally assist minimize porosity problems.
Another sophisticated remedy involves making use of sophisticated welding tools. Making use of tools with integrated attributes like waveform control and advanced power sources can enhance weld other quality and decrease porosity dangers. The implementation of automated welding systems with precise control over parameters can significantly minimize porosity flaws.
Moreover, integrating sophisticated tracking and assessment innovations such as real-time X-ray imaging or automated ultrasonic testing can aid in detecting porosity early in the anchor welding procedure, allowing for instant rehabilitative activities. In general, integrating these advanced remedies can substantially enhance porosity control and enhance the overall top quality of welded components.
Verdict
In final thought, recognizing the science behind porosity in welding is necessary for welders and fabricators to create high-grade welds - What is Porosity. Advanced services for porosity control can better enhance the welding procedure and make certain a strong and trustworthy weld.
Report this page